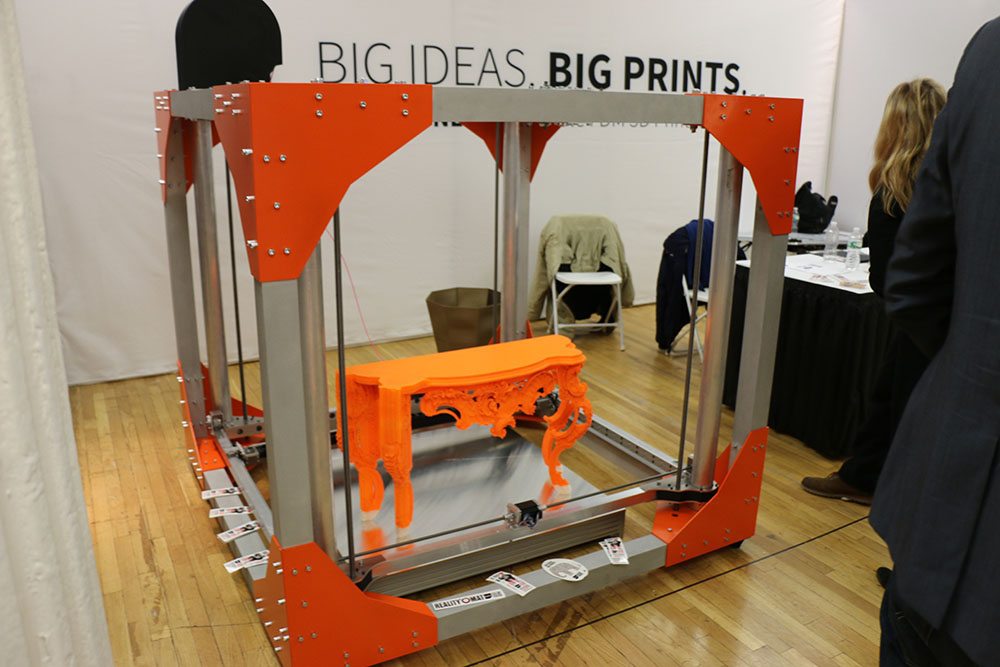
Photo courtesy of Guilechat, Wikipedia
3D printing has made great advances in recent years and has opened doors in the field of technology. 3D printing, also known as additive manufacturing, was created in 1984.
Currently, Ramapo College owns a 3D printer open to all students for academic and personal use.
The Harvard Business Review, or HBR, recently covered the growth of the 3D printing movement – in 2014 the industry grew by 35.2 percent – and its role in advancing the capabilities of medical technology.
The advantages of 3D printing include its relative cheapness and small margin of error, because the 3D printed items are assembled directly from a digital model, which increases the precision rate and therefore reduces the margin of error, according to HBR. The technology differs from previous manufacturing techniques that rely on methods such as cutting, drilling and chopping. Such methods increase waste and extraction costs, which are not present in the 3D printing process.
Freshman Daniel Sclafani, the student lab aide in charge of Ramapo’s 3D printer, is knowledgeable and enthusiastic about the emerging technology. The plastic Sclafani uses in the College’s lab is known as PLA. “It’s a plant-based polymer that is entirely nontoxic and biodegradable,” said Sclafani, who abstains from using another popular plastic, ABS, “which is a synthetic polymer, which is what Legos are made of. But we do not use that because it’s not as friendly.”
The 3D printing process can be described as “a hot glue gun on a track that has three axes,” Sclafani explains.
3D printing’s use in the health care field represents the industry’s most important contribution to science, according to Sclafani: “It’s the biggest thing that 3D printing has done for us, like prosthetic lenses.”
Recently, 3D printers have created airway splint implants for children and are manufactured to grow in size with the patient. The splints successfully tested on three patients between the ages of infants and toddlers as of April 2015. According to HBR, the splints cost $10 each.
Princeton scientists used 3D printing technology to create a bionic ear that can hear radio frequencies better than the average human ear. The ear was produced within a project “to explore the feasibility of combing electronics with tissue,” HBR states. This was the first public effort to build a fully functional organ. And according to the researchers, “the field of cybernetics has the potential to generate customized replacement parts for the human body” and can create organs more capable than the average human organs.
Therefore, 3D printed livers, kidneys and lungs are not merely a fantasy for related patients and their loved ones – those 3D organs can become reality and will reduce the long donor lines and increase the number of related survivors.
The 3D printing industry not only has shown potential to create organs, but has developed cost efficient methods of cancer treatment. According to the HBR, back in 2014, researchers developed a fast and inexpensive way to make facial prostheses using facial scanning software and 3D printing for eye cancer patients who underwent surgery.
Moreover, the HBR reports that in 2015, researchers discovered the potential for printing customizable biodegradable implants to increase efficiency when curing bone infections and cancer.
Over the past few years, 3D printing has shined a bright light in areas of health care that were dark in hope for treatments and cure.
ppark1@ramapo.edu